Identifying Waste for a Lean Distribution Center
Over recent years, I have been asked on occasion if you can apply Lean principles in a warehouse or distribution center (DC) environment. The simple answer is yes. However, applying Lean to a DC is not as straightforward as it is for manufacturing operations. Lean is simply eliminating waste from processes that do not add value and about which your customers don’t care–harsh, but a reality. Lean requires a shift in thinking and approach; hence, “Lean Thinking” requires executive support from the top down.
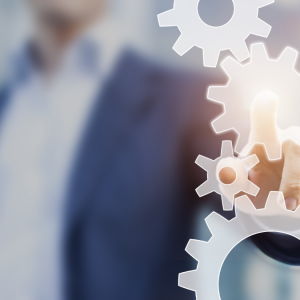
Integrating Lean Process Improvement
Research has shown that nearly 70% of continuous improvement projects, such as Lean or Six Sigma, fail to achieve their organizational goals.
The Seven Wastes of a Distribution Center
Here are the seven types of waste in a distribution center environment.
- Defects Defects are a wasted effort to create something the customer rejects. This forces added waste management processes. For example, shipping an incorrect SKU on an order or the incorrect quantity.
- Over-Processing Using anything (materials, resources, unwanted features) that are more expensive than needed by the customer results in waste. For example, the concept of Lean time replenishment is waste. There is nothing Lean about topping off a forward pick location with unnecessary inventory and allocating resources to complete the tasks.
- Over-Production More production or acquisition than is needed, generally to hide production problems results in excess inventory. Although many distribution center environments do not actually have manufacturing production processes, many distribution centers have kitting (single deep bills of material).
- Unplanned Inventory, Raw Materials, Work-in-Process, or Finished Goods If value is not being actively added, even for a small period of time, this is waste. Unfortunately, many distribution center leaders do not control the actual purchase planning, so they wind up managing some amount of dead inventory. It is important that you measure the value of your inventory and report monthly on inventory that is obsolete. A good carrying cost number to use is 12-15%.
- Inspection Waste occurs each time product or an order is inspected. For example, auditing a direct-to-consumer order prior to shipping is waste. Your goal should be “One Touch, Right Time, First Time.”
- Waiting Waiting time wasted by workers waiting for resources or waiting for a pull signal. Waiting often leads to additional non-value-add processes to manage that waiting. For example, equipment or employee congestion in an aisle is waste.
- Motion Motion of the worker or equipment that does not add value is waste. As many of you know, travel distance (walking) is the largest labor cost component in a DC. Therefore, a focus should be eliminating unnecessary distance and time moving from location to location (forward pick or reserve locations).
Unlike manufacturing where Lean can be implemented with little to no technology, distribution does require some level of technology (reference illustrations below). We have created a “Lean in the Lean” methodology focused on eliminating waste utilizing Kaizen Blitzes, Value Stream Maps and Key Metrics to drive waste out of distribution centers.
Lean Road Map
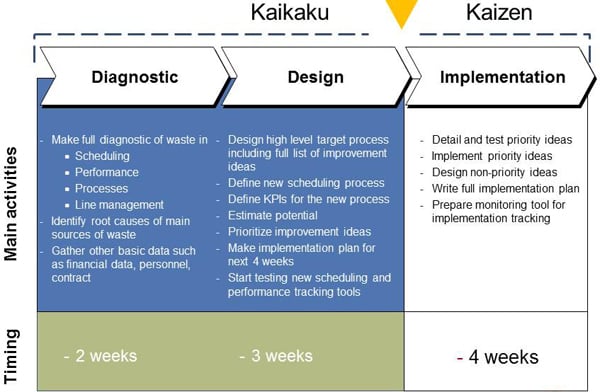
enVista takes Lean seriously and has 70 trained and certified consultants. We also teach and can certify clients in Lean. There is always room for continuous improvement.
Scope of Deployment
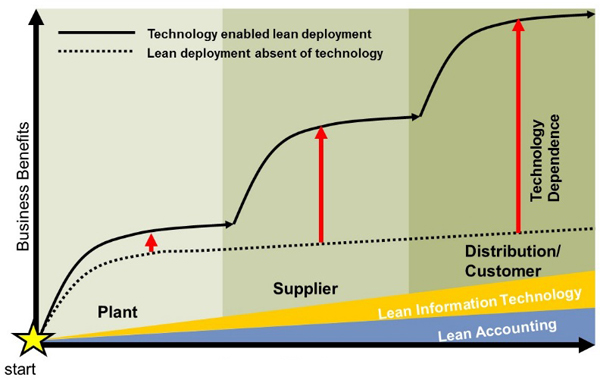
Please reach out to us if you have questions about how to apply Lean principles to your DC. Also, be sure to read our white paper, Integrating LEAN Process Improvement.