I worked recently with a customer focused on improving worker performance and productivity. This customer had implemented a variety of compensation plans with their current work force and wanted to benchmark their current productivity against best-in-class LEAN operational processes. During our observation of the customer’s current inbound unloading and receipt staging process, enVista’s team noted that our customer had implemented a very successful team-oriented approach aimed at maximizing productivity thru cooperative accountability. The name of this type of cooperative compensation and work force alignment is “pool pay.”
The idea of pool pay for this company’s inbound freight handling process consists of a group of workers, typically eight on a shift, who are incented to properly unload and receive as many trailers in a given shift as possible. The incentive is driven because the group will earn a specific flat amount into their “pool” for each trailer unloaded; each member of the group receives an equal share of the pool pay amount. The on-site group supervisor does have the ability to alter the percentage a specific team member receives which helps guard against a group member purposely slacking off compared to other group members; a change to the pool amount must be thoroughly documented and have the signed consensus of the other group members.
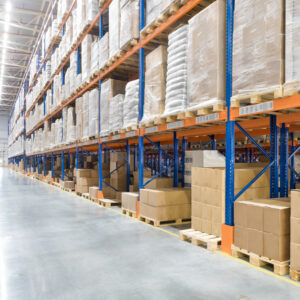
Increase ROI Through Successful Warehouse Slotting
A well-thought-out slotting strategy also enables businesses to minimize wasted space and maximize storage capacity within the warehouse. Increase ROI using the right tools, strategy and management plan with successful warehouse slotting.
enVista’s team observed the “pool pay” concept consistently over a three day period across multiple shifts and consistently found the following results:
- The role each worker has during unloading and receiving process rotated by day, as decided upon by the group members. When asked to describe the value of this rotating assignment each team member consistently responded that this helped each member better appreciate the holistic task required by the team to complete a successful trailer unload and receipt. The team members also said that working the same role day in and day out would be monotonous while rotating provided them opportunities to work with different equipment (e.g. forklifts, pallet jacks) as well as technology (e.g. data collection devices, bar-code scanning). Our team also observed new roles that had evolved thru trial and error, green-light thinking, and open group member suggestions, all in an effort to expedite and improve the quality of their process. In one example, a new position had been created for specific loads where the received pallet quantity had to be broken-down into dynamic permutations assigned that day; the worker would mark each received pallet with a specific separation line thus facilitating a fluid process from unload to final stacking.
- The team functioned consistently with LEAN processes that minimize non-valued added product handling and touches. At the time of this writing, every team in the unloading and receiving process, across all shifts had gone fifty-five weeks without an incident or accident. What is even more amazing is that over 80% of the work-force had less than one year with the organization as this was a new site operation for the company.
- There was a consistent level of pro-active collaboration across active loads from all team members. The on-site supervisor would originally assign one or more group members to a specific load to begin the process, but when one load experienced a delay (ex. waiting for a specific piece of material handling equipment) the group members assigned to the load instinctively went to another load to assist without having to be told to do so. By comparison, enVista has observed organizations that pay individuals or teams by a specific load; in these environments there is ownership by the group to the load, but only that load since these workers are not financially incented to assist another load.
In summary, consider the above-mentioned points when determining how to staff your new operation, as well as an option to consider in your existing operation to generate better productivity, a consistent awareness of dependent upstream and downstream processes to your current job, and implement LEAN best practices that are safe and efficient.