In recent years, there has been considerable debate about whether modern goods-to-person (GTP) item picking is superior to more traditional person-to-goods (PTG) item picking. Each picking methodology has its pros and cons, but how do they compare, and is one superior to the other? First, let’s define each system.
What is a Goods-to-Person (GTP) System?
A goods-to-person system is a type of warehouse automation technology that uses robots or other automated machines to move items from storage to the workers who are picking them for orders. This type of system is designed to improve efficiency and accuracy in the picking process and can be used in a variety of settings, including e-commerce fulfillment centers and traditional warehouses. In a GTP system, the automated machines bring the items to the workers, rather than the workers having to travel to the items, which can save time and reduce the physical demands of the job.
What is a Person-to-Goods (PTG) System?
A person-to-goods system is the opposite of a goods-to-person system, in which workers travel to the items that need to be picked, rather than the items being brought to them. In a PTG system, workers typically use carts or other devices to move around the warehouse and pick items from their locations on the shelves or in storage bins. This type of system is common in traditional warehouses and distribution centers and can be less expensive to implement than a GTP system, which often requires the use of expensive automation technology. However, a GTP system can be more efficient and can help to reduce errors in the picking process.
Goods-to-Person & Person-to-Goods: Benefits & Disadvantages
Both systems have their place, but they each have distinct advantages and disadvantages to consider.
Goods-to-Person System
Benefits:
- Higher Efficiency – Reduces worker travel time and increases picking speed.
- Lower Labor Dependency – Reduces reliance on manual labor and mitigates labor shortages.
- Improved Accuracy – Automated retrieval systems reduce human error.
- Better Space Utilization – Stores goods more densely and uses vertical space effectively.
Disadvantages:
- High Initial Cost – Requires significant investment in automation and infrastructure.
- Complex Implementation – Requires careful planning and integration with existing systems.
- Limited Flexibility – Harder to adapt to rapidly changing inventory needs.
- Potential Downtime Risks – System failures or maintenance issues can disrupt operations.
Person-to-Goods Systems
Benefits:
- Lower Initial Investment – Typically requires less capital expenditure on automation.
- Flexibility – Easier to adapt to changes in demand and product types.
- Scalability – Can scale by adding more workers rather than investing in automation.
- Simple Implementation – Easier to set up and integrate with existing operations.
Disadvantages:
- Higher Labor Costs – Requires more manual labor, leading to increased costs over time.
- Slower Picking Speed – Dependent on human efficiency, which can limit throughput.
- Increased Fatigue & Errors – Workers walking long distances can lead to fatigue and mistakes.
- Space Inefficiency – Requires wider aisles and more open space for human movement.
Despite the increased attention and coverage of goods-to-person order fulfillment systems over the past few years, they are not a new concept. Goods-to-person systems have been around for decades, but recent technologies and software advancements have enabled significant improvements in functionality, efficiency, inventory management and space utilization. However, many companies are not fully convinced that GTP integrated systems are reliable, and that they can effectively deliver acceptable ROI.
On the other hand, an increasing number of distribution and warehousing professionals are starting to believe that PTG technologies and order fulfillment methods are somewhat outdated in modern distribution environments. Large warehouses, SKU proliferation and smaller order fulfillment windows are rendering PTG processes less effective due to increased picking travel, mis-picks and increased labor requirements.
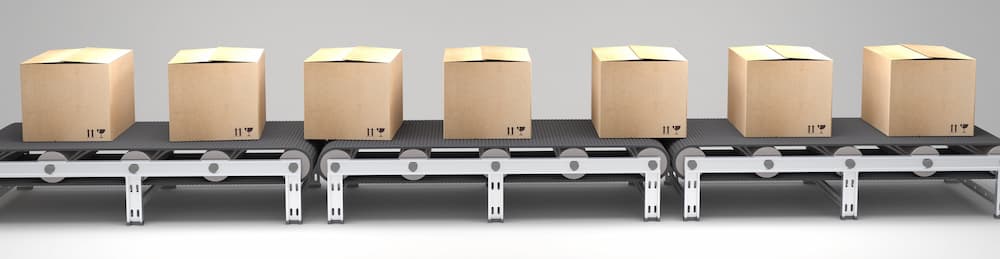
Which System is Right for Your Needs?
To determine the order fulfillment system that best fits your specific business requirements, a careful review of the following operational considerations is key:
Order Picking Travel Time
There is no doubt that eliminating travel time for order picking can increase productivity. GTP operations definitely have the edge here over PTG operations, but not every distribution operation will realize similar benefits. Small facilities or very densely slotted pick engines will benefit less due to the shorter distances that employees are required to cover. When it comes to GTP and reduced travel time for picking, the larger your facility and picking engine, the greater the benefit.
Order Accuracy
GTP system providers frequently point to increased accuracy as a major differentiator for their technologies. This reasoning is based on the idea that GTP automated retrieval systems deliver the correct product directly to order pickers’ workstations, reducing the opportunity for mis-picks. Real-world data confirms that most GTP systems easily exceed 99-plus percent order accuracy.
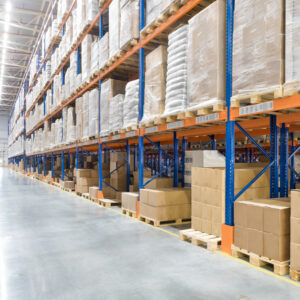
Increase ROI Through Successful Warehouse Slotting
A well-thought-out slotting strategy also enables businesses to minimize wasted space and maximize storage capacity within the warehouse. Increase ROI using the right tools, strategy and management plan with successful warehouse slotting.
Smaller Footprint/Better DC Cube Utilization
Within GTP operations, automated retrieval systems can be more condensed horizontally than traditional PTG picking/order fulfillment systems. This allows for a smaller footprint even when compared to the most condensed PTG order picking modules or Very Narrow Aisle equivalents. Keep in mind that the need for dedicated pick/put workstations in GTP operations can reduce this horizontal footprint advantage to some degree. The real benefit of GTP systems, however, is unparalleled vertical space utilization.
Single Point of Failure
Today, GTP ASRS technologies are tremendously accurate and productive. However, if the GTP automated storage and retrieval system goes down due to a catastrophic mechanical or software failure, manual access to inventory contained within can become nearly impossible. An entire order fulfillment operation can come to a grinding halt. Automated PTG systems are certainly not immune to malfunction, but the easy accessibility to pick facings can allow order fulfillment operations to continue to function at some level despite the loss of automation.
Capital Expenditure
Typically, GTP systems with ASRS are much more expensive than automated PTG systems. The level of automation, equipment and software required for fully automated GTP systems can often result in capital expenditures that are 100 percent higher than PTG equivalents. Yet, despite the initial capital expenditure differential, in some operational environments, GTP systems have the potential to generate excellent ROI when factoring the potential labor productivity efficiencies, real estate savings and life cycle costs.
Product Sequencing
If your distribution operation requires ‘aisle-ready’ totes or pallets, or its SKU mix requires intelligent product placement within an order container to accommodate weight distribution, grouping by product category or another logistics purpose, you are likely already familiar with product sequencing.
Conclusion
When it comes to deciding between a GTP and a PTG order fulfillment solution for your distribution operation, there is not a single, clear-cut solution. There are many factors that must be considered before arriving at the order fulfillment solution best suited for your business. It starts with a comprehensive understanding of your current order fulfillment operation and data. Effective utilization of this data to identify operational weaknesses is critical. From there, companies must determine which business initiatives are most aligned with the organization’s long-term goals. Is labor cost reduction a bigger priority than improving time to customer? Is establishing new sales channels more important than SKU proliferation? How a company prioritizes strategic initiatives plays a large part in determining the best order picking system.
Ultimately, operational metrics provide the backbone for the initial data analysis and operational self-assessment. Strategic business initiatives and long-term goals provide a detailed roadmap forward. It’s only when today’s data and tomorrow’s direction are analyzed in unison that the ideal balance between optimum order fulfillment system performance and maximum return on investment can be achieved.
For more information on the factors to consider when determining the right order fulfillment solution download our white paper.