How to Plan for a WMS Implementation
Planning a WMS implementation can be an overwhelming task. There are so many moving parts (pun intended) that it’s important to know what you’re getting into and how to best mitigate risks to project failure or going over budget.
Having managed hundreds of WMS implementation projects in the last 15 years, we have 8 tips to share with you to help ensure a successful WMS implementation.
1: Set Expectations for the Project
Companies often believe that the warehouse management system itself is the solution to all their problems. Other critical elements end up being ignored or not taken into account such as slotting considerations or how responsibilities for an associate are going to change from what they do today.
There are many implications to consider across warehouse operations that impact both people and processes. What used to be manual work changes as efficiencies are realized once the warehouse management system is in place.
To make sure you set the right expectations, ask yourself:
- Do I need a warehouse management system?
- What’s the right type of warehouse management system?
- What’s the role that system is going to play in our warehouse operations?
- How will my team’s work change day-to-day?
2: Consider Who Will “Own” the Warehouse Management System
Identifying the internal team that will be responsible for the success of your new warehouse management system seems obvious, but it’s often overlooked. Getting this team involved from the beginning of the project is critical to overall project success.
Normally, the best department to own the system is the Operations Department. The reason for this is that the Operations Department is going to be the final user of the system when the WMS implementation is complete, and it becomes accountable for the change management process. Allowing the Operations Department to own the system from the very beginning ultimately ensures that it will benefit from the system once it gets rolled out.
3: Plan Your WMS Implementation Timeline
You always want to be thinking at least 3-5 years out when you’re planning your warehouse management system project.
For instance, if you currently fulfill for retail in one warehouse but have plans to do e-commerce in the future, understanding how your business might change in the future is very important in considering enabling technology and system requirements that will support your omnichannel fulfillment capability.
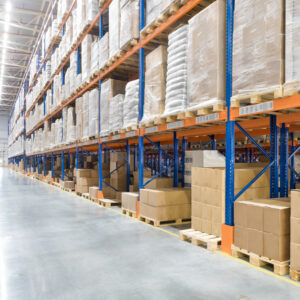
Increase ROI Through Successful Warehouse Slotting
A well-thought-out slotting strategy also enables businesses to minimize wasted space and maximize storage capacity within the warehouse. Increase ROI using the right tools, strategy and management plan with successful warehouse slotting.
4: Get Your IT Team Involved in Your WMS Project Early On
There are many considerations that IT will need to weigh in on. For example:
- Do you want to have the system on premise?
- Do you want to put it in the cloud or have it hosted by somebody outside the organization?
- What’s the right database structure and operating system?
- What are all the systems that are now going to have to interact with this new warehouse management system?
IT has a critical role, not only up front, but through the course of the warehouse implementation as well.
5: Determine Your Requirements Before Starting the Vendor Selection Process
One of the biggest tips is to make the project a customer led process, not a vendor led process. There are many situations where customers bring vendors in, and they haven’t defined what their requirements are. They simply ask the vendor to tell them what they are good at and how that may apply to their business.
A more effective process is doing your due diligence upfront to understand the role of the warehouse management system in your operations. Then you can lead each vendor through very detailed requirements and scripting capabilities that say exactly how you want your system to be able to interact within your IT ecosystem. You also get a chance to connect the dots as an organization to see how it all effectively works together and aligns with your business goals.
6: Avoid Modifications to Control Project Costs
Don’t modify the system. Beware of scope creep. It’s been our experience that upwards of 70 percent of developed modifications are either unnecessary or are replaced with future system upgrades. Stick to the base! Change your processes, as necessary. Base implementation risks are significantly reduced (risks of cost over-runs, schedule delays, future upgrade difficulties and costs). Also, once the initial design is completed and agreed to, be adamant about not allowing significant changes, as these will invariably extend the timeline, add cost, and introduce higher risk.
7: Incorporate Testing, Training, and Go-Live Elements into Your Project Budget
Project components that often get missed are ones that occur when the transition starts happening, things like testing, training and go-live. As part of the change management process, the software vendor will start moving more responsibility over to the customer, and the customer needs to incorporate this phase into the project cost.
The customer has to make sure that they have the resources and the time for that transition. Most projects fail in these final steps when people haven’t done a thorough job of testing specific requirements. When resources are not thoroughly trained, they can be the main factor of project failure once the warehouse management system goes live.
There’s also the go-live support. If you’re a 24/7 type of operation, make sure that you have people that are available to help support you during those first two weeks. The success of a WMS implementation is going to be strongly influenced by those first two weeks.
8: Manage Project Scope Instead of Forcing Shortcuts
In general, shortcuts are typically looked down upon. There’s always the question of how to do things faster. You have time, you have resources, you have costs, and these things have to be managed.
One of the things that is encouraged when looking for potential shortcuts is to not try to do the same amount of work in a shorter amount of time. That can have some risk associated with it, so try to pare the scope down a little bit instead. Phased implementation still allows you to get the value a little quicker while helping you achieve the overall goal and scope that you want.
Doing Your WMS Implementation the Right Way
Taking the time up front to consider your system requirements and plan your project goes a long way to following the Do’s and Don’ts of WMS Implementations. Make sure to remember these key considerations, and you’ll be on your way to a successful warehouse management system implementation project.
- Take the right amount of time to design exactly where you think the warehouse management system will have a role within your operation.
- Look at IT capabilities, functional requirements, and any type of cost-benefit analysis because there are a lot of options out there.
- Make sure that this is a process led by you and not a vendor led process. They’re working for you, and you’re in the driver’s seat. Pick the system that will meet your needs.
- You can’t ever do enough testing or training. Informing the organization as to why you’re making this change, what’s the benefit to the organization, who’s going to be involved, and what the long-term benefits are going to be could be a 2-3 year process from start to finish.
If you’ve got a warehouse management system project on the horizon, we invite you to reach out to our team. enVista has over 15 years of experience implementing warehouse management systems from the best vendors in the industry.
Let’s have a conversation.