Business leaders are constantly facing operational challenges and striving for improvements within their supply chain. In a recent Supply Chain Digest survey, reducing supply chain costs was identified as the top priority for 57 percent of executives. One of the ways this can be accomplished is by eliminating operational inefficiencies from the supply chain. However, this becomes a difficult undertaking because the underlying causes of operational inefficiencies are often difficult to identify and require significant time, effort, and resources. Whether the issue is known or not, an operational assessment is an effective tool to ensure supply chain improvement initiatives are addressing the root issue – rather than its symptoms.
An operational assessment is an evaluation of the day-to-day operations within a specific area of a company’s supply chain, such as warehousing or transportation processes. The key objectives of an operational assessment are to recognize and correct operational inefficiencies, as well as provide solutions that enhance future profit margin. When maximizing profit, it is important to remember that a 10 percent decrease in bottom-line costs boosts profit significantly more than a top-line 10 percent increase in revenue – it is paramount that cost-centers like warehouses are operating efficiently. An operational assessment will typically include an onsite interview of key stakeholders to identify key pain points as well as a Lean process analysis which helps identify “low-hanging fruit” that will produce quick wins.
Operational assessments take time and resources to execute effectively – underscoring the importance of performing an operational assessment only when it adds value. There are several reasons why a firm may utilize an operational assessment:
- Failure to meet cost and/or service expectations of the business
- In order to enable changes in response to shifts in corporate objectives
- Shifts in the business landscape (e.g., corporate merger, new market opportunities, changing demand preferences, etc.)
- To act on a benchmarking assessment that uncovered an underperforming portion of the business
Operational assessments provide data-driven conclusions that lead to measurable, tangible, and financially viable solutions. The bottom line value of any operational assessment is the knowledge that comes from it. Insight into the underlying causes of problems within a firm is invaluable to decision-makers. Also, operational assessments frequently uncover low hanging fruit that can drive immediate savings – many times with little to no upfront capital expenditures – as well as other actionable items geared toward long-term strategic goals. The relatively low upfront cost of an operational assessment provides an inexpensive way to discover where future investments are or are not needed.
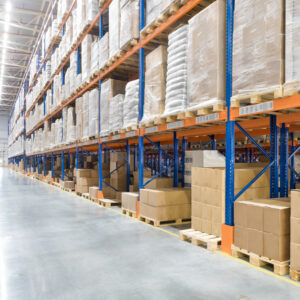
Increase ROI Through Successful Warehouse Slotting
A well-thought-out slotting strategy also enables businesses to minimize wasted space and maximize storage capacity within the warehouse. Increase ROI using the right tools, strategy and management plan with successful warehouse slotting.
All successful operational assessments follow a common methodology that includes the following steps:
- Understand the current operating environment
- Establish the requirements
- Identify opportunities to drive operational value
- Design for the future
Operational assessments are useful in troubleshooting pain points that an organization is experiencing. They help managers understand what their top concerns should be and provide valuable insights about the unknown, often uncovering cost reduction and service level improvement opportunities.
For more information on different types of operational assessments and how they can provide a bottom-line benefit to your organization, check out enVista’s white paper Diagnose Your Supply Chain Challenges with an Operational Assessment.