It’s well-known in the grocery industry that the average profit margin on an order is between 1-3 percent. There are many factors that determine this margin, including competing grocery chains, store infrastructure costs, and transportation and distribution-related costs associated with receiving and shipping products. All of these are led by consumer demand.
Grocers rely heavily on a high-volume and differentiation of products. They also adopt today’s latest pickup or delivery service offerings, such as Home Delivery Services or Click & Collect channels, commonly referred to as Buy Online & Pickup in Store (BOPIS), to get food from their stores into their customers’ shopping carts.
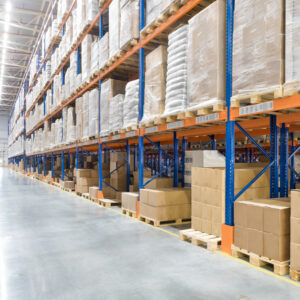
Increase ROI Through Successful Warehouse Slotting
A well-thought-out slotting strategy also enables businesses to minimize wasted space and maximize storage capacity within the warehouse. Increase ROI using the right tools, strategy and management plan with successful warehouse slotting.
Reduce Labor Costs in the Distribution Center
So why is labor and employee productivity of such concern to the grocery industry? Because it all starts in the distribution center, which represents a large opportunity for cost savings initiatives, such as process improvement through Lean strategies, process and technology improvements, and labor management systems (LMS) programs.
All three of these types of programs listed above have one thing in common: the distribution associates and their need for training and frequent feedback on their contributions to the overall performance of the distribution center, thereby driving down costs and increasing profit margin.
Some of the biggest challenges in today’s world of logistics are recruiting, onboarding, and retaining talent in order to continue to grow market share. According to Peerless Research Group’s 2019 Materials Handling Technology Study, “only 17% of companies have implemented a Labor Management or workforce management program in their distribution network with 21% planning to evaluate, purchase, or upgrade in the next 24 months.”1
Companies who have successfully implemented LMS programs have experienced productivity gains on the order of 10 to 20 percent, as noted by Dan Gilmore, Editor of SupplyChainDigest, in his popular blog on Supply Chain Solutions offering the Best Pain to Gain ratios.2
Discover Opportunities to Increase Profit Margin
With over 300 Lean, Process Improvement and Labor Management implementation projects, enVista’s Industrial Engineering and Labor Management professionals can assist grocers in reducing operating costs, thereby increasing profit margins within your supply chain and retail store network.
Interested in learning more about Labor Management? Here is a whitepaper on 8 Real World Lessons Learned from an LMS Implementation.