Process mapping is the core of all lean organizations. It’s the foundation of your business and it’s the map to your success or your demise. So often I work with organizations that do not have a clear understanding of their processes. I’m not talking about Value Stream Mapping, Standard Operating Procedures or even Preferred Methods. I mean a process map, in its most basic form. I like to think of process documentation in a pyramid format, with Process mapping at the foundation and Preferred Methods at the peak.
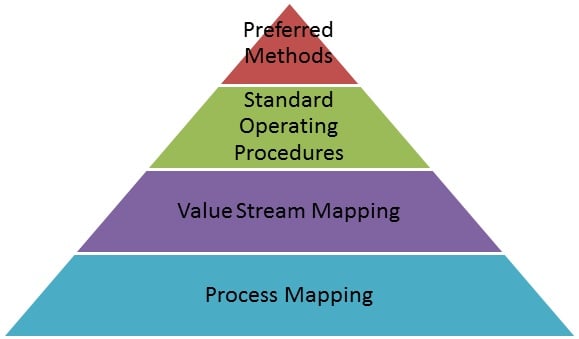
Over the course of the next four blogs, I will be focusing on core steps to complete the above pyramid successfully. All organizations that have a Lean focus should complete these steps immediately. If your organization has completed some of these tasks, but not all, then start where your organization has left off. If your organization already has these in place, it’s a great time to review these documents as processes continue to change and adapt to the ever-changing business environment and customer demands.
Overview: Process Mapping
A process map is at the heart of every organization and defines what tasks must be completed in order to produce any output. Whether it is accounting, human resources, operations, or customer service, everything involves a process and it should all be documented.
Some Basic Definitions:
Task: Steps that must be performed in order to complete a process. Example: Placing a label on a carton.
Process: A collection of tasks that are needed to turn an input into an output. Example: Picking, Hiring, Invoicing.
There are many methods to developing process maps:
- Management walking around the warehouse and following workers to get a good understanding of the tasks needed to define a process.
- Hiring a consultant to walk around your operations, interview your staff, and then deliver a diagram of the tasks that define a process.
- Establishing a task force of workers to complete the above two methods.
While all of those methods work in defining your processes, I have come to enjoy (and so have my clients) Brown Paper Process Mapping.
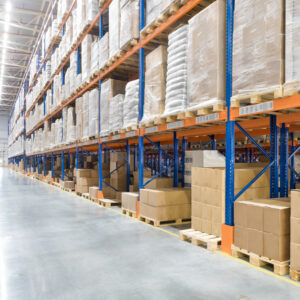
Increase ROI Through Successful Warehouse Slotting
A well-thought-out slotting strategy also enables businesses to minimize wasted space and maximize storage capacity within the warehouse. Increase ROI using the right tools, strategy and management plan with successful warehouse slotting.
Overview: Brown Paper Process Mapping
Brown Paper Process Mapping involves physically mapping your business and operations processes on a conference room wall on a very large sheet of brown paper with Post-it® notes. Each Post-it® note color serves a purpose:
Green – Individual steps in the process
Yellow – Decision Points
Pink/Red – Opportunities
Clients that use this process really prefer it over the traditional methods of process mapping for several reasons:
- The entire company gets involved in the process.
- Warehousing, accounting, sales, purchasing, and transportation associates are all involved in the process.
- Each team has an hour to interact in the room and document the processes that they use every day.
- It gives a very holistic view of the processes involved in running your day-to-day operations.
- It is visually appealing. All of the different color post-its mean something different, making opportunities easy to identify at a quick glance.
- It provides a hands-on exercise that energizes your internal workforce to begin finding opportunities to improve their processes and company processes overall.
- Associates are able to identify how their processes interrelate to other areas of the business and creates a sense of ownership and quality.
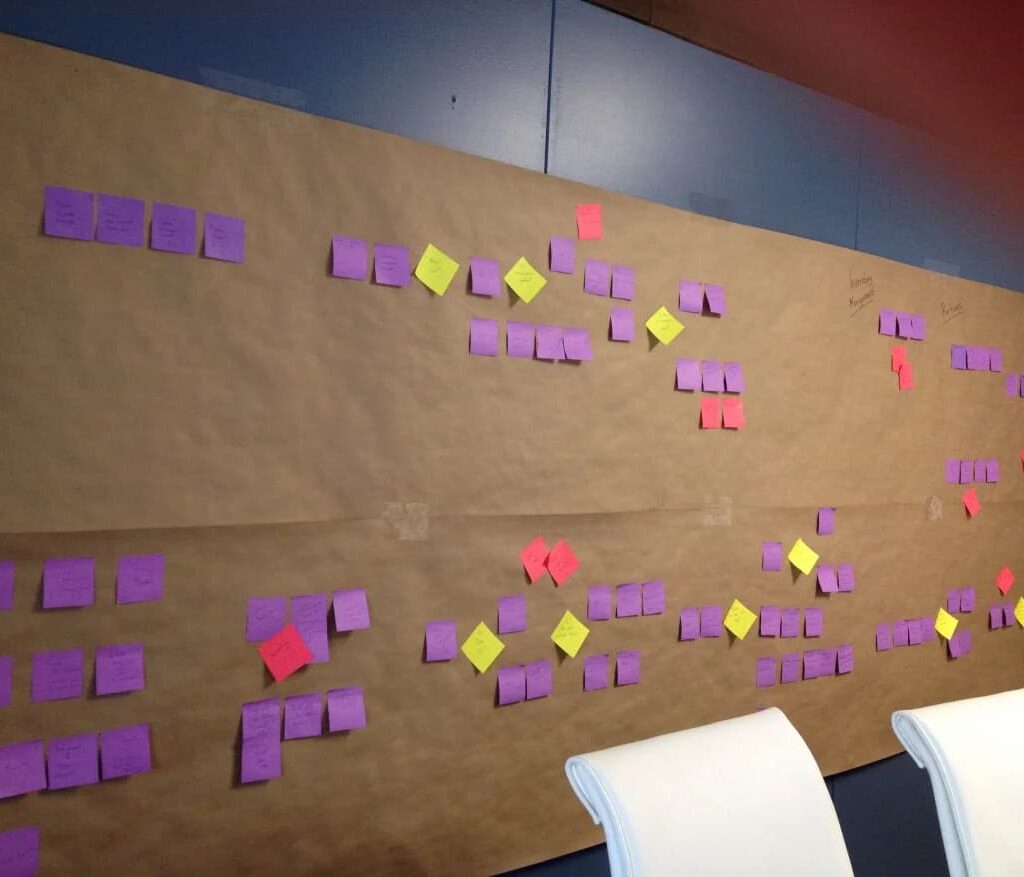
Conclusion:
Once you have concluded your Brown Paper Process Map, you’ll need to get the processes down on paper. The easy way to document processes is by using Microsoft Visio. Place one process on each tab of Visio and distribute them to the appropriate process owners for review. Make any updates that are needed and get ready for Phase Two: Value Stream Mapping.