Learn how to leverage process mapping and Pareto analysis for inventory optimization
Well, OK, maybe not rigorous Upper Control Limits and Lower Control Limits statistically defined for the process of maintaining Inventory Accuracy. Interesting thought though, right? At what incidence of fully accurate counts would you want to alert that something is out of control (!)? A hundred in a row, and we start to get suspicious? Ten?
But, hopefully, you get the point. It’s not about finding inventory counts in error and fixing them. It’s about characterizing the processes that lead to inventory being accurate or inaccurate. And then improving those processes for greater accuracy.
Remember that what we are seeking is repeatable and consistent high quality transaction execution exactly the goal of all quality improvement techniques.
Cross-Functional Process Improvement
All the techniques we’ve learned for process and quality improvement can come into play:
Recognize that inventory accuracy is not solely in the domain of Warehouse Management. Like most significant opportunity, it’s going to take multi-function teamwork to effectively address. For example:
- Quality as mentors and (perhaps) managing the cycle counting activities.
- Engineering and Manufacturing Engineering for clean item definition. and change management/revision control as well as accurate BOMs (especially if there is any material back-flushing).
- Production control/materials management/shop floor as customers of accurate inventory.
- Warehouse management team who are at the core of this.
- Purchasing for clear item identification (on receipt).
- Cost Accounting/Finance, at the very least, because we want to educate them on quality processes over full physicals.
Truth be told, I’ve never worked with a good Cost Accountant who didn’t know better than anyone how things are being done today and what transactions can be trusted and which can’t.
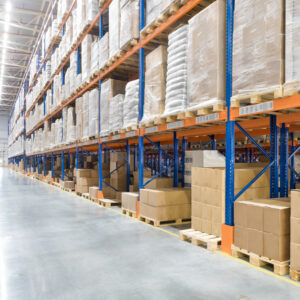
Increase ROI Through Successful Warehouse Slotting
A well-thought-out slotting strategy also enables businesses to minimize wasted space and maximize storage capacity within the warehouse. Increase ROI using the right tools, strategy and management plan with successful warehouse slotting.
The 5 Ws of Process Mapping
Mapping existing processes that entail any inventory movement or transaction.
The quality of the transaction. Clear transactions. Reliable part identification. Trained operators. The what and how.
Are the transaction boundaries clear and crisp? Where are the weak points? Where are the transaction delays and queues (my favorite target)? When is movement transacted where?
Where do authority and responsibility not match? Who is and who should transact? Are they clearly accountable and properly lead? What’s the incentive for doing it right and doing it better?
Measurement and Pareto Analysis
Measure the improvement opportunities. Which sources of inaccuracy might provide the greatest accuracy improvement for the least cost and effort? Apply Pareto analysis, using the 80-20 rule to identify the next most rewarding process improvement opportunities.
Form team(s), brainstorm, develop, characterize and justify solutions. Establish measures and controls to track progress.
Institutionalize, declare solved and start over with the next most fruitful looking initiative.
Notice all this emphasis on process measurement. When we are measuring the inventory accuracy of processes, we really are talking Cycle Counting. Properly, it is the statistical analysis of those processes. It is much, much more than correcting count discrepancies. It is THE tool for diagnosing and surfacing the process sources of those discrepancies.
Conclusion
The traditional approach of Pareto classing all inventory activity to identify A, B and C class items, counting/sampling the A’s more frequently than the B and the A’s more frequently than the C’s makes total sense. But, even then, most companies don’t routinely count even the A’s more than once a month. And this tends to be more justified to pacify Finance that it’s a reasonable substitute for a full physical – each item is guaranteed to be counted at least once a year. It’s hard to diagnose a discrepancy back to the source when you only look once a month.
If we’re monitoring the processes that lead to error, we really need to focus on a smaller target with higher frequency. I like to use what I call a Control Group here. As the Team processes process flows, brainstorms, measurements, and, especially, as start gleaning precious feedback from disciplined cycle counting, those targets will identify themselves. Identify representative target items and, frankly, count the heck out of them maybe daily. You stand a much better chance of catching a juicy cause.
Once we’ve worked our target and improved the processes based on implemented solutions, seek the next target, and thus the next cycle count control group.