One of the approaches enVista helps customers review during any type of supply chain initiative is to review your current operation for increased efficiency. Supply chain projects are the ideal time to examine non-valued added steps as well as possibly address the cliché question, “Why does our organization do it this way?”. Studies have shown that companies who automate bad processes actually increase their cost of operating largely due to two factors:
- Automating a process with technology that enforces checks and balances will most likely add steps to your process in order to capture data points or perform validation checks within a process that already has more steps than it needs.
- Adapting a solution to meet a companys inefficient process most likely leads to customization and modification of the technology, again leading to additional implementation and support costs.
Part of the reason operational process changes are not implemented as part of a supply chain initiative is that most software vendors identify these tasks as “client-side” services, left to the initiation and discretion of the customer to execute, not the software vendor. Accordingly, most vendors will help support the configuration and setup of any customer supply chain, even those that are sub-optimal, with the guarantee that the software will work as defined and configured. Unfortunately, the uneducated customer who has not implemented these systems before can be easily mislead that the software by itself will act as a panacea to current operational challenges.
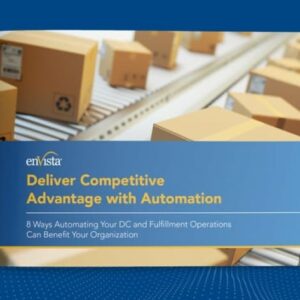
Deliver Competitive Advantage with Automation
Discover the eight operational considerations when determining whether automating your distribution center is right for your organization.
Case in point, I visited an electronics manufacturer and distributor who was eight weeks into an implementation of a new tier-1 warehouse software application. The customer asked that enVista help review their current product slotting because they were consistently short shipping orders because the required items were not available in the designated primary location, in this case level one racks. The customer sited that they could not complete and execute replenishment tasks in time for picking to be executed, so clearly they did not have items located in close proximity to their associated level one primary location. I watched one of the company’s top workers execute a typical replenishment transaction, which averaged fifteen (15) minutes to complete (4 replenishments per hour compared to an industry best practice of 10 per hour). The replenishment worker was spending significant time letting down multiple partial pallets of the same item from a reserve location and manually consolidating this into a single replenishment pallet.
I could understand during the first week of implementation where the warehouse system would try and flush out excessive “honeycombing” (i.e. storing multiple partial pallets of the same item in many reserve locations caused by pickers randomly allocating product from the closest location to them, not necessarily the oldest), but not after eight weeks. I went back to review the receiving process and the locating rules associated with new item receipts; almost every container shipment resulted in a single partial pallet remaining after unitizing the product on the receiving dock. Accordingly, in following the company’s original process, all pallets received, including both full and partial, were first located to an empty location rather than trying to consolidate like product together, (NOTE: this product is not date sensitive), the software system emulated exactly the original process the company had before, but the process was not efficient and was causing significant challenges downstream.
One solution for the customer is to focus on better processes up front during receiving and put-away to help create increased throughput and order fulfillment downstream. No question that slotting would also help the client, but a thorough examination of all their processes was immediate; then the software could be configured to support these efficient processes as opposed to “better sameness.”