Value can be quite difficult for many companies to define. What is value? Value is always defined from the customer’s perspective. Do they perceive a process or step in the process as creating or producing value?
If the answer is yes, then the step is considered to be value-added. If the answer is no, then the step is considered non-value added. Does that mean that you can eliminate all non-value-added steps? Not exactly.
Value Add vs. Non-Value Add
To determine if steps are value add steps, you must ask yourself a few questions.
- Does the customer value this output? Would they be willing to pay a premium for the task?
- Were there errors with the output? Any re-work or verification steps don’t add value. The real question is: Why was it not done correctly in the first place?
- Did the output change? Has the output or product been altered by going through this step in the process?
By asking the questions above, companies can quickly determine if steps are value-added or non-value-added. Unfortunately, not all non-value-added steps can be eliminated. There are different types of non-value add:
- Required Non-Value Add: These are tasks that the customer may not directly consider value, but the company or government entity needs them. An example might be internal tracking purposes or government regulations, such as lot numbers or EPA reporting.
- Unrequired Non-Value Add: These steps are known simply as waste and add absolutely no value to the company, government or customer. These steps should be eliminated immediately.
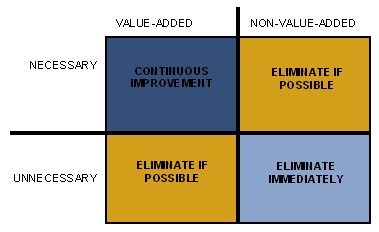
What is Value Stream Mapping?
Value stream mapping refers to the sequence of events required to design, produce, and provide a specific good or service to a customer. Value streams occur in all areas of a business, not just on the production floor.
The process of outlining these tasks will quickly bring to light any inefficiencies and waste that are keeping businesses from performing at their best. By utilizing the questions above and identifying whether a step is value-added or non-value-added will get you one step closer to developing your own value stream map.
Start by going through each task on your brown paper process map and ask the three questions outlined above. Tasks that are non-value added should be circled on their respective Post-it® notes.
Several members throughout the organization should review these tasks and determine if these tasks are in fact required. There are many tasks that some groups may think are unnecessary but are in fact needed by a particular department within the organization.
If it is determined that all departments agree the step is non-value-added and not required, a red Post-it® note should be placed over the Post-it® that lists the unnecessary step. This will give your team a visual as to how many steps are currently not required and non-value-added. A team member should be assigned from each department affected by these non-value activities and work on eliminating them immediately.
If a step is determined to be required, this should also be denoted on value stream mapping documentation. Doing so will assist the team in reevaluating these steps in the future to determine if the task is still required.
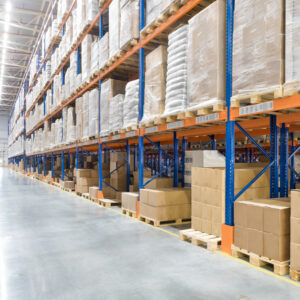
Increase ROI Through Successful Warehouse Slotting
A well-thought-out slotting strategy also enables businesses to minimize wasted space and maximize storage capacity within the warehouse. Increase ROI using the right tools, strategy and management plan with successful warehouse slotting.
Conclusion
Once everything is classified as value-added or non-value-added, it’s important to document the entire process using Visio or a similar program. Use color codes to assist in the value stream mapping process:
- Value Add = White
- Non-Value Add but Necessary = Yellow
- Non-Value Add and Unnecessary = Red
Once documented, you will need to distribute the value stream to all impacted departments for review. A formal document will need to be created, explaining how unnecessary non-value added steps are going to be eliminated from existing processes.
Next, create a project plan and roll-out to the appropriate teams for execution. Then continue to monitor the changes to ensure they are in fact unnecessary.