The design of a warehouse significantly impacts the efficiency of put walls, which are crucial for sorting items during order fulfillment. A well-planned layout positions put walls near the end of the picking process to reduce worker travel time and streamline sorting. The size and shape of the facility determine the number and placement of put walls, ensuring optimal space utilization. Integrating automation, such as conveyors or robots, into the design enhances sorting speed and accuracy. A flexible warehouse layout also allows for easy scalability as order volumes grow.
What is a put wall?
A put wall is a system of shelves designed for order consolidation, picking and packing productivity improvement and order fulfillment accuracy. Items are batch-picked and brought to the operator at the put wall, where they are scanned and placed into cubbies for specific orders. A light notification system guides the operator, and once an order is complete, the cubby light signals to the packer that it’s ready to be packed.
Put wall systems provide many key benefits for distributors:
- Scalable and reconfigurable as your business needs evolve
- Paperless
- Real-time visibility and control
- 100% scanning quality check
- Ergonomic design
- Take up minimal space
Put walls are an alternative order picking process. They are a centralized, flexible point for picking and order consolidation. This system allows for combining lines from multiple customer orders for simultaneous order fulfillment. Put walls are ideal for e-commerce and other direct to consumer (DTC) sales channel order fulfillment and are suitable for wholesale and B2B small order fulfillment.
Put walls are key to efficient order consolidation, and their effectiveness is heavily influenced by facility design. A well-designed layout ensures a smooth flow from picking to the put wall, minimizing travel time and boosting throughput. The number and placement of put walls depend on the warehouse’s space utilization, with strategic positioning maximizing productivity. Integrating automation can further streamline the process, while a flexible design allows for easy scaling of put walls as order volumes increase.
Reduce Errors and Increase Efficiency with a Put Wall System
The ever-increasing number of online orders and heightened customer expectations has led to the order fulfillment process becoming more and more complicated. When it costs nearly six times more to gain a new customer than to retain a current one, retailers cannot afford a misstep in the shipping process. Customers are placing more and more orders for more and more items. Retailers must be prepared to fulfill each of these orders, even when parts of the order are uncommon. Along the same lines, this SKU proliferation has led to the diversification of order and product profiles. Organizations must be prepared to ship small items and large items, in large or small quantities. These factors and more have led to retailers integrating put walls into their fulfillment execution strategy in order to reduce errors and increase efficiency.
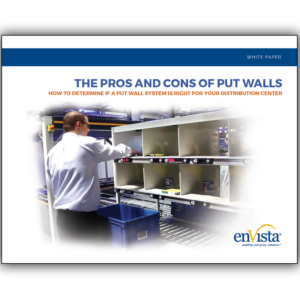
The Pros and Cons of Put Walls
Put wall picking is becoming more common in order fulfillment. Read enVista’s unbiased evaluation about the pros and cons of put wall systems
Benefits of Put Walls in Facility Design
Put walls offer significant benefits in facility design by improving order fulfillment efficiency and accuracy. They streamline the picking process by reducing travel time, as items are batch-picked and brought directly to the operator. They optimize the packing process by providing a dynamic system for indicating when an order is ready to be packed. This goods-to-person system minimizes labor and handling, increasing productivity. With their organized cubby system and light notification feature, put walls ensure accurate order consolidation. Additionally, put walls can easily scale to meet growing order volumes, and their integration with automation enhances sorting speed, further optimizing warehouse operations.
Scalable, modular and moveable
Put walls can grow or shrink as the distribution center needs. During the peak season when many more individual orders are being fulfilled, the put wall setup can expand to meet the distributor’s needs. During other times, the put wall can shrink back down or be moved to a different area of the distribution center. Recent advances even allow for the put wall shelving to be modified to be larger or smaller as needed.
Increased employee productivity
Put walls allow for greater productivity because operators are more stationary. They can fulfill more orders more accurately and their movements are more ergonomic. Put zones may be turned off and multiple lights may be used so that more than one operator can operate in the same zone. Cycle times are also improved with put walls because more than one put wall can be operating at once which results in less time to get a large number of orders completed.
Increased order accuracy
Scanning items as they are sorted, and relying on a put to light system allows for 100% in-line quality check which maximizes order accuracy rates.
Minimal barriers to entry
While put walls can be used in conjunction with specialized materials handling equipment such as conveyors or an AS/RS, they are not required. A put wall system can be implemented with the bare minimum of static shelving, put lights, and RF scanners. This makes put wall implementation very cost effective.
100% paperless
Because put walls rely on scanning and a lighting system, there is no paper. This provides several different benefits: less potential for trash in the distribution center, less confusion for operators, and provides a sustainable solution for the distribution center.
Maximized use of space
Put walls result in excellent physical order staging and consolidated order density. A typical system contains dozens of cubbies in a small area and the cubbies are constantly cycled through as orders are completed and they are emptied so they may be packed.
In conclusion, put walls play a vital role in optimizing order fulfillment processes, offering numerous benefits when integrated into facility design. By reducing travel time, minimizing errors and enhancing productivity, they streamline the entire picking and consolidation process. The scalability and flexibility of put walls allow warehouses to efficiently meet fluctuating order volumes, while their ergonomic design improves employee efficiency. With minimal barriers to entry and a paperless system, put walls provide a cost-effective and sustainable solution. As e-commerce and direct-to-consumer demands continue to grow, reaching nearly $2 Trillion USD of revenue in 2024, put walls will remain a key component in enhancing warehouse operations and supporting the evolving needs of modern supply chains.
If you’re looking to optimize your warehouse operations with effective facility design, contact us today for expert consulting services. Our team can help you implement the right solutions to improve efficiency and scale with your business needs.