We are all very aware of the current economic struggle facing most organizations in the country today. In an effort to combat slumping sales, companies are rationalizing their internal expenses to include site closings, employee layoffs, and eliminating unnecessary travel; all of this I understand. But companies are also using this economic trend to put on hold capital projects previously justified to reduce costs within their organization withi a reasonable period of return and payback; this I don’t understand.
Most companies embark on supply chain cost savings initiatives because they believe in the opportunity to reduce transportation cost, inventory carrying costs, non-value added processes, and inefficient labor. So why not continue with these cost cutting initiatives?
If funding for these initiatives was reliant upon lending institution financing, which is now more difficult to get, I understand the need to look at alternative cost cutting measurements, ideally those that are foundation builders with the larger initiative in mind. But if you are an organization stock-piling cash because of uncertainty in the market, stay the course and understand that executing in the present time will help you drive savings that much sooner.
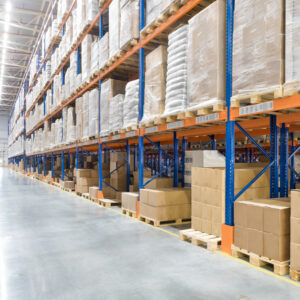
Increase ROI Through Successful Warehouse Slotting
A well-thought-out slotting strategy also enables businesses to minimize wasted space and maximize storage capacity within the warehouse. Increase ROI using the right tools, strategy and management plan with successful warehouse slotting.
If you haven’t exercised a strategic planning process for your organization, it does not have to be costly or time-consuming (typically executed within 4-8 weeks); realistically, you have valuable resources internally who can allocate their time to this study and execution during these slow times, thus helping to reduce your capital cost. Remember the cost to recover from making a poor or reactive tactical decision can be more expensive then the cost of a strategic assessment. Here are some potential short-term cost savings activities (and their conservative cost savings percentages) for you to consider in conjunction with a simple labor percentage reduction:
- Transportation Contract Management (~ 5% Savings on Current Freight Spend for Applicable Carriers)
- Transportation Freight Auditing (~ 2% Savings on Current Freight Spend for Applicable Carriers)
- Labor and Performance Management (~ 11-13% Savings on Current Labor Spend for Applicable Business Units)
- Product Slotting Analysis (~ 5-10% Improvement in Warehouse Space Utilization)
In terms of “soft” cost savings initiatives that are more difficult to attach hard dollar savings to, but can be executed quickly and cost effectively, consider:
- Assess your current operations and existing technology for a best-practice wellness check-up (Typically Two-Days To Complete)
- Stakeholder and Supervisor-Level On-Site Supply Chain Operation Education and Certification (Typically One-Three Days Depending Upon the Class Agenda and Content)
If you are a stakeholder or executive from companies experiencing these expense rationalization decisions, I want to hear from you and understand why these proven initiatives could not work in your company.