Updated: 7/3/18
Uncover Significant Opportunities for Waste Reduction and Productivity Improvements
The lean methodology has widely been applied to supply chains, manufacturing, lean warehousing and distribution. But what happens when you apply lean processes thinking to your retail store operations?
Lean or kaizen events are often applied in the distribution center to drive out waste. But there is also opportunity for organizations to hold these lean events in retail stores, connecting your value stream from the store all the way back through to your distribution and company’s vendors’ supply chains. Applying lean to retail stores can uncover significant opportunities for waste reduction and productivity improvements.
The 5 Principles of Lean
- Identify value from the customer perspective
- Map the value stream
- Create flow – make the steps that create value flow in tight succession
- Establish pull – let customers “pull” value from the next upstream activity
- Seek perfection – rinse and repeat the process until the process occurs with no waste
How do you apply these lean principles to retail stores? enVista’s Kurt Leisman shares his top 10 tips on using lean in retail stores.
Tips to Incorporate Lean Retail for Your Organization
1. Leverage meaningful data
There are several KPIs you need to know to make meaningful improvements to reducing waste. Do you know how long your queue is? How long on average it takes to service a customer? How long it takes to unload a trailer?
Lack of actionable data leads to additional waste in the form of additional time spent gathering baseline data and metrics. You need to make sure your data is in order so your lean decisions are based on facts.
2. Define what improvements in productivity are based upon
Improvements in productivity are based upon understanding best practices, preferred methods, and standards.
- Best practices are defined as the optimal material flow strategy and equipment to meet customer demand.
- Preferred methods are the optimal way to perform an individual task.
- Standards are the engineering standards for each of the work methods that feed you labor allocation and scheduling system.
Poor methods or process should not be optimized. Simply discard them.
3. People can’t be controlled like machines
People are your major assets, but they are also your major cause of variation and will often resist change that’s imposed on them. Pay particular attention to people concerns at the beginning of a project.
4. Track flow in a retail store
In a retail store, the concept of tracking material flow can be difficult. It’s more difficult to stand in a store and watch material flow like you can on the warehouse floor.
Products and services do flow. You just need to use tools like a Value Stream Map and Customer Journeys to see them. Start with the customer and go all the way back to your supplier.
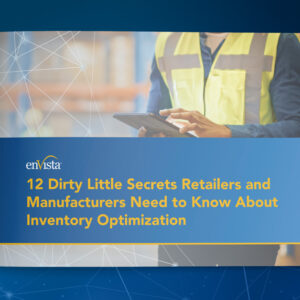
12 Dirty Little Secrets Retailers and Manufacturers Need to Know About Inventory Optimization
Get the low-down on the secrets retailers and manufacturers need to know about inventory optimization.
5. Don’t let lean terminology be intimidating
Simplify and conform lean terminology and methods to match your current terminology. You already have your own culture and common language so leverage this and translate lean to your own terms when possible. You’ll gain traction across your organization more quickly.
6. Include store associates in process improvements
Store associates are often given guidelines of how their work should be performed, but they generally have room to structure their daily tasks and make their work their own. This individual control over certain components of in-store work can lead to resistance to defining process improvements in their domain.
People can fear losing whatever creativity and freedom they have in being able to do their job the way they see fit. The only way to get your associates to accept process change more smoothly is to involve them in what to change and how to change it. Include them on lean teams and empower them to help create best practices, preferred methods, and standards as you seek to eliminate waste.
7. Learn how to recognize waste
Retailers often have not been trained to observe their processes to identify the eight types of lean waste. The 8 types of lean waste include: defects, overproduction, waiting, non-utilized talent, transportation, inventory, motion and extra processing.
Start viewing your business using this lean waste filter. You’ll be amazed by what you see.
8. Identify variability in retail functions
There is always a great amount of variability in every aspect of retailing (sales forecasting, inventory control, task management, etc). With lean, you’ll need to identify the variability in your business and then apply the lean toolbox to reduce the variability
Ultimately, this will help drive down cost. At a retail store, this may mean trailer shipments that can be processed with the same size staff.
Where variability cannot be reduced, seek to increase your flexibility. In stores, this could translate to cross training employees.
9. Focus on standardization
Complexity exacts an enormous cost on store processes. Because of this, you’ll need to focus on standardizing components and sub-processes as much as possible. Use the “KISS” principle (Keep It Simple) when developing your preferred methods and SOPs.
Standardizing will go a long way to help reduce process and service complexity.
10. Leverage lean teams to identify opportunities and craft solutions
A kaizen event will use common sense to improve cost, quality, delivery and responsiveness to your customer’s needs. A kaizen event lasts one-week and uses small cross-functional teams who seek to improve a process or problem identified within in a specific area in a very short period of time (“Quick Wins”).
Conclusion: enVista Lean Retail and Supply Chain Services
enVista’s team of supply chain experts are lean certified and deeply experienced in improving and optimizing supply chain performance. One way we do this is lean operations consulting in both distribution center and retail settings.
Do you need help improving your performance and eliminating waste? Check out our supply chain operations services.