How to Improve Your Supply Chain Cost Management
To CFOs, supply chains are a tremendous cost of doing business and a potential drain on profitability. It doesn’t have to be that way. The best supply chain leaders are those who can control supply chain costs in the face of disruptions like recessions and pandemics. They focus on aligning and improving key supply chain operating outcomes to optimize costs and improve overall supply chain strategy.
Here are 8 proven tips every CFO should be aware of to better understand where costs can be saved and revenue increased through improved supply chain cost management practices and technology.
1. Supply chain visibility can reduce the uncertainty that inflates safety stock – and improve budgeting and cost control
Since problems and disruptions happen everyday, managers at each supply chain node add safety stock to help ensure they can maintain service levels. While you can’t stop problems from happening, by giving managers visibility to these disruptions sooner, and by providing visibility to alternate sources of supply and distribution, managers can react more quickly with more certain results to keep the supply chain flowing. This can significantly reduce the uncertainty and the need for large buffers of safety stock.
2. Best practices and Engineered Standards can significantly reduce labor costs
Industrial engineers can examine all of the tasks in your distribution centers and stores to determine the most efficient method to perform each task and set standards for how long each task should take. Then, workers can be taught the best way to perform their tasks. A Labor Management System will track worker performance against the engineered standards and notify supervisors of which associates may need more training and coaching to achieve their goals.
3. Good Labor Management reduces hiring costs
Good labor management through engineered standards coupled with accurate monitoring and personalized coaching leads to greater job satisfaction, improved morale, and reduced turnover, meaning reduced hiring and training costs.
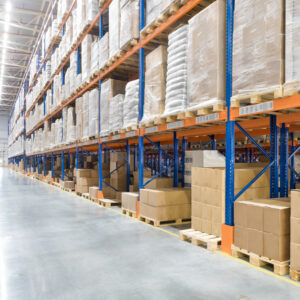
Increase ROI Through Successful Warehouse Slotting
A well-thought-out slotting strategy also enables businesses to minimize wasted space and maximize storage capacity within the warehouse. Increase ROI using the right tools, strategy and management plan with successful warehouse slotting.
4. Better efficiency reduces capital requirements
Once you have reduced inventory levels and increased worker productivity, you can accomplish more work within existing facilities using existing equipment. As your business grows, you are more likely to be able to handle the increases without adding more equipment or facilities, thus reducing your capital expenditures.
5. Optimize transportation practices to reduce transportation costs
Moving products across today’s global supply chains is no easy task. A robust Transportation Management System can handle all aspects of transportation and provide extensive logistics order management that enables supply chain visibility. It will enable optimization of inbound and outbound moves and ensure efficient consolidation and routing, and execute the transportation plan with low-cost portal-based carrier integration, as well as Electronic Data Interchange. The result is reduced transportation cost and more predictable, reliable service.
6. Improved vendor management increases in-stock inventory, sales and customer service
Many retailers try to manage their suppliers through chargebacks. Savvy retailers are leveraging technology to turn inbound transportation data from suppliers into actionable insight to mitigate non-compliance before it occurs. Taking a more strategic approach benefits both retailers and suppliers in the form of more accurate, on-time order deliveries, and improved customer service.
7. Improved service increases revenue
It’s no secret that improved service leads to more satisfied customers. Happy customers are likely to continue buying from you. Thus, the supply chain improvements we have been describing not only reduce costs but also lead to higher revenue.
8. Improved supply chain management can better support omnichannel operations
In today’s omnichannel environment, companies cannot adequately fulfill customer needs across channels without advanced supply chain management practices and technology. Inventory optimization and supply chain network analysis are important tools to address and optimize omnichannel practices. By understanding demand patterns across channels, companies can better plan for and deliver against demand.
All of the benefits discussed in these tips to control costs can be realized sooner by outsourcing the strategy, implementation, and hosting to vendors who specialize in these areas. They will understand the software and the implementation “gotchas” that only come from experience, which saves your staff time, reduces implementation problems and allows you to start earning returns faster.
Partner with enVista to create a supply chain cost optimization vision that drives performance improvements and cost efficiency.